Get inspired
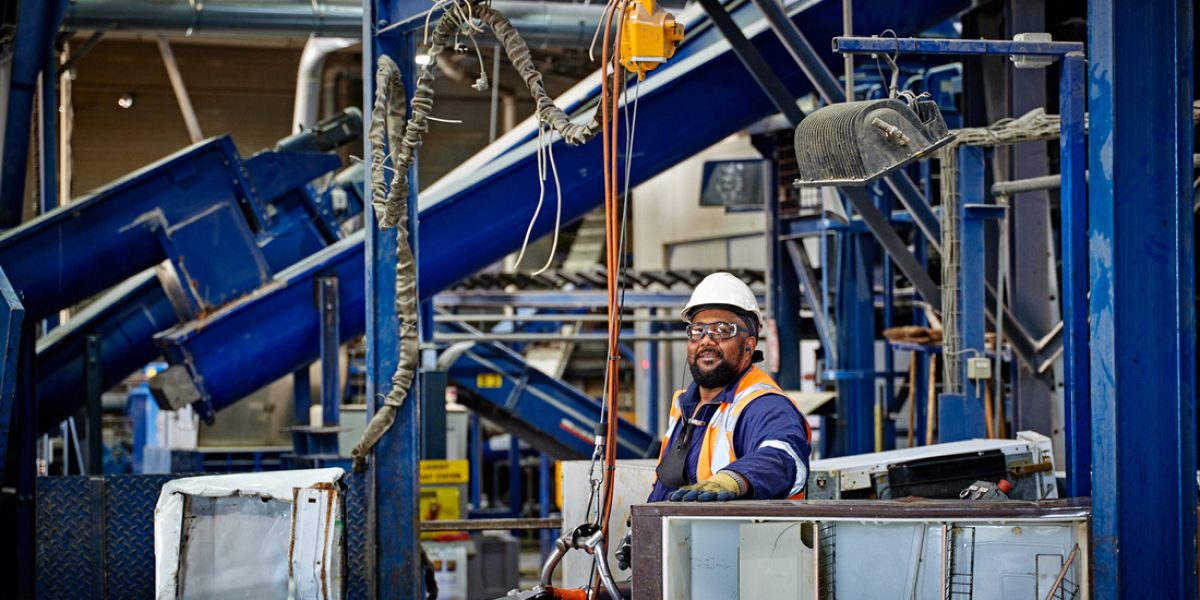
HKS Metals is an important partner of Wecycle and one of the largest processors of e-waste in our country. The company is working hard to meet the European collection target of 65% by persuading as many parties from the metal recycling sector as possible to have their material recycled at HKS. But an uncompromising commitment to ever purer output streams also works to the advantage of producers and importers, because this automatically leads to higher recycling percentages. Nevertheless, sufficient challenges remain – if only because new generations of appliances are coming onto the market faster than ever before. Stefan van der Wekken, Managing Director at HKS talks about it.
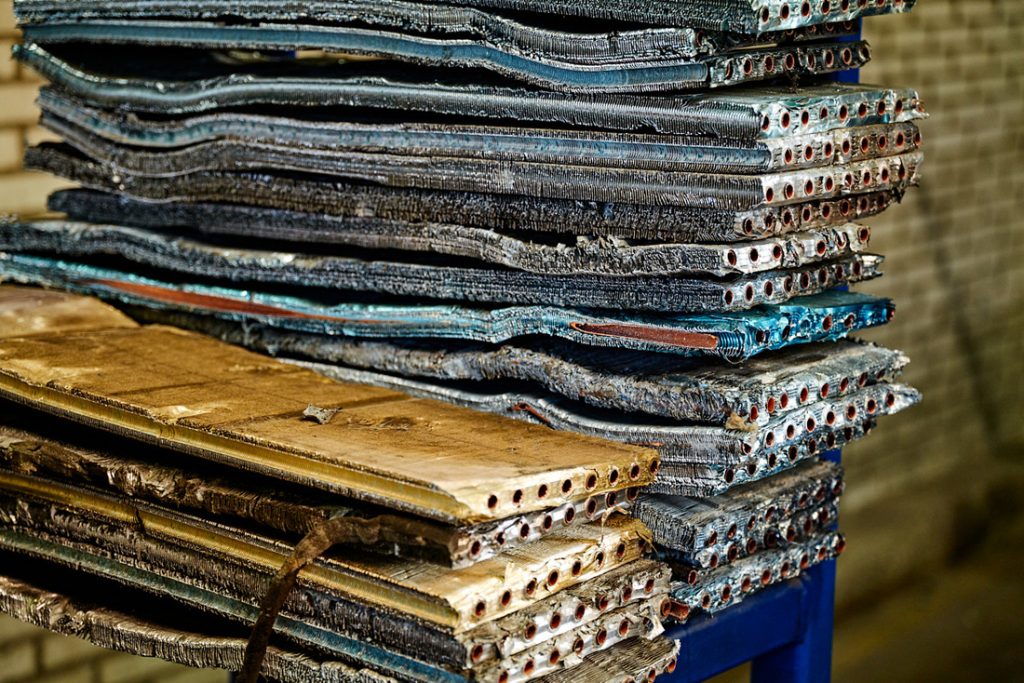
For the whole of 2020, HKS Metals processed slightly more e-waste than in the previous year. But those figures do incorporate a huge spike during the first lockdown, says Stefan van der Wekken, Managing Director at HKS. “I’ve been in the business for about 20 years, but I haven’t seen anything like this before. At the same time, we had to pull out all the stops to guarantee the continuity of our business processes. We succeeded by acting very quickly and by strictly following and enforcing the RIVM guidelines. E-waste recycling is very much manual work, so we had to provide the right protective equipment and information for employees, rearrange the workshops and in a number of locations we even had to build new canteens and changing rooms to meet the 1.5 meters guideline. It was all very radical, but it allowed us to continue to serve our customers, including Wecycle.”
New technologies
HKS is not only one of the largest recyclers of e-waste in the Netherlands, but also one of the most ambitious. “We really work from the intrinsic motivation that recycling contributes to caring for people and the environment,” says van der Wekken. “And as far as we are concerned, it can be even more sustainable. On the one hand, by reducing our own energy consumption per ton of recycled material and reducing the number of manual operations through mechanization and automated processing. On the other hand, by investing in new technology so that our output streams are so pure that we can sell them directly to end processors in Europe. This is completely successful for metals, but not always for plastics and other residual materials. Composite plastics, laminates, glued components: the recycling sector will continue to face many challenges in the years ahead. We are not running away from them and we are developing new technologies and solutions for them.”